Hon Hai Precision Things To Know Before You Get Thiss
Wiki Article
Hon Hai Precision Can Be Fun For Everyone
Table of ContentsDie Casting Can Be Fun For AnyoneThe Main Principles Of Lean Production Additive Manufacturing for BeginnersThe Greatest Guide To Die CastingThe 8-Second Trick For Plastic ManufacturingManufacturing Things To Know Before You Get This
The message on this page is a sample from our complete White Paper 'Shot Moulding for Buyers' - * Example message * - for complete guide click the download button above! Introduction This overview is meant for people who are wanting to source plastic mouldings. It offers a much needed insight into all that is included with producing plastic components, from the mould tool required to the moulding process itself.If you desire to discover even more, the guide covers sorts of mould devices, in addition to special ending up procedures such as colours & plating. Words that are underlined can be located in the reference in the appendix ... Component I: Moulding: The Essentials The Benefits of Injection Moulding Plastic injection moulding is a very accurate process that provides a number of advantages over other plastic processing techniques.
Precision is perfect for very detailed components. Compared to various other methods, moulding enables you to incorporate more functions at very little resistances. Look at the photo to the right. hon hai precision. You can hold this moulding in the palm of your hand and it has bosses, ribs, steel inserts, side cores as well as holes, made with a sliding turned off function in the mould tool.
Not known Details About Plastic Manufacturing
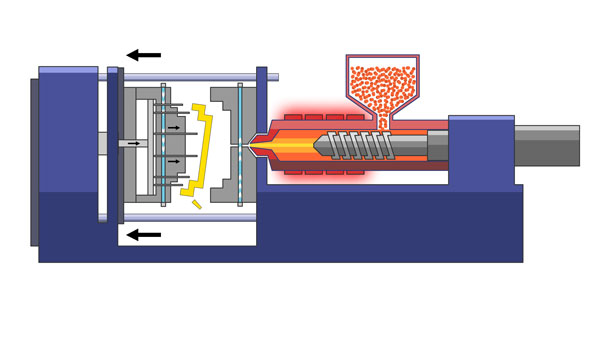

from material feed & melting; material injectionProduct cooling time and ejection as well as the re-closing of the mould tool ready device the next cycleFollowing Draft angles - The walls of a moulded part must be somewhat tapered in the instructions in which the component is expelled from the mould tool, to permit the part to be expelled easily.
Ejector stroke - The pushing out of ejector pins to eject the moulded part from the mould device. Ejector stroke speed, length as well as timing needs to be meticulously regulated to prevent damage to the ejectors and also mould tool, but at the same time make the moulding cycle as short as possible.
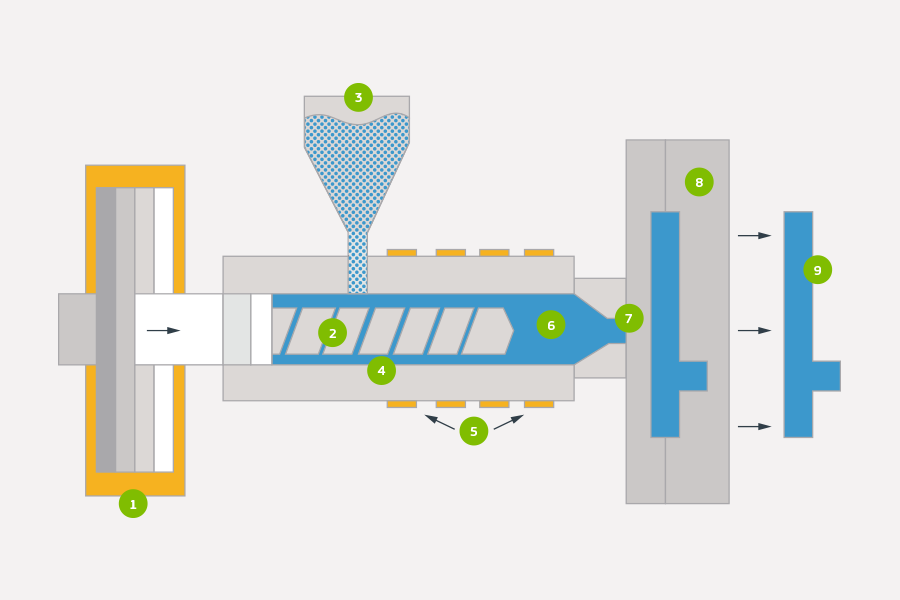
A Biased View of Additive Manufacturing
Ribs - When a plastic part has thin walls, ribs are contributed to the design to make the slim walls stronger Side cores - Side action which produces a function on a moulded component, at an opposing angle to the normal opening instructions of the mould tool. lean production. The side core needs to be able to withdraw as the plastic part can not be ejected or else.
Walls - The sides of a moulded component The text on this page is an example from our complete White Paper 'Injection Moulding for Customers'.
Manufacturing procedure for generating parts by infusing liquified material right into a mould, or mold and mildew Streamlined representation of the procedure Injection moulding (united state spelling: shot molding) is a production procedure for producing components by infusing molten material right into a mould, or mold. Shot moulding can be carried out with a host of products mainly consisting of steels (for which the procedure is called die-casting), glasses, elastomers, confections, as well as the majority of generally polycarbonate and also thermosetting polymers. Injection moulding is commonly used for making a variety of components, from the tiniest elements to entire body panels of vehicles. Injection moulding makes use of a special-purpose device that has 3 components: the injection device, the mould and the clamp.
What Does Oem Mean?
, with the quantity used of asml euv the previous being significantly higher.: 13 Thermoplastics are common due to qualities that make them extremely suitable for injection moulding, such as simplicity of recycling, flexibility for a broad variety of applications,: 89 and also ability to soften and stream on heating.In multiple dental helpful site caries moulds, each cavity can be the same as well as develop the very same parts or can be special and create numerous different geometries throughout a solitary cycle. Moulds are typically made from device steels, however stainless steels and aluminium moulds appropriate for particular applications. Aluminium moulds are typically improper for high quantity production or components with narrow dimensional tolerances, as they have inferior mechanical residential properties and also are much more susceptible to wear, damages, and contortion throughout the injection as well as securing cycles; however, aluminium moulds are cost-efficient in low-volume applications, as mould construction costs as well as time are significantly reduced.
When enough material has gathered, the material is forced at high pressure and velocity into the part forming tooth cavity. The exact quantity of contraction is a function of the resin being utilized, and can be fairly foreseeable. To avoid spikes in pressure, the process usually makes use of a transfer position representing a 9598% complete tooth cavity where the screw changes from a continuous speed to a continuous stress control.
Rumored Buzz on Manufacturing
Once the screw reaches the transfer position the packing pressure is applied, which finishes mould dental filling and makes up for thermal shrinkage, which is quite high for thermoplastics about several other products. The visit this page packing stress is applied till eviction (dental caries entry) strengthens. Due to its little dimension, eviction is generally the starting point to solidify with its entire thickness.: 16 Once eviction solidifies, no even more product can get in the cavity; as necessary, the screw reciprocates and obtains product for the following cycle while the product within the mould cools down to make sure that it can be expelled and be dimensionally steady.Report this wiki page